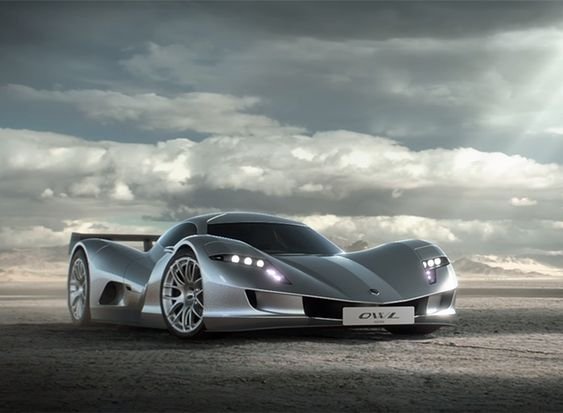
The automotive industry has been a significant adopter of robotics technology for decades. From the early days of simple assembly line robots to today’s advanced, AI-driven systems, robotics has played a pivotal role in transforming how vehicles are designed, manufactured, and maintained. In 2024, the landscape of robotics in the automotive sector continues to evolve at a rapid pace, driven by advancements in artificial intelligence (AI), automation, and digital technologies. This article delves into the key trends shaping the integration of robotics in the automotive industry, exploring how these innovations are driving efficiency, enhancing safety, and transforming the manufacturing process.
1. Collaborative Robotics (Cobots)
One of the most significant trends in the automotive industry is the increasing use of collaborative robots, or cobots. Unlike traditional industrial robots, which are typically large and require safety barriers to operate, cobots are designed to work alongside human workers in a shared workspace. This collaboration between humans and robots is transforming the automotive production process, making it more efficient and flexible.
Key Benefits of Cobots:
- Safety: Cobots are equipped with advanced sensors that allow them to detect human presence and stop or slow down to avoid accidents. This makes them safer to work around than traditional industrial robots.
- Flexibility: Cobots can be easily programmed and reprogrammed, making them ideal for handling a wide range of tasks, from assembly to quality control.
- Cost-Effectiveness: Cobots are generally more affordable than traditional robots, making them accessible to smaller automotive manufacturers.
In 2024, cobots are being used for tasks such as installing car components, welding, painting, and performing quality inspections. Major automotive manufacturers like BMW, Ford, and Volkswagen are leveraging cobots to streamline their production lines, reduce downtime, and enhance worker safety.
2. Artificial Intelligence and Machine Learning
Artificial intelligence (AI) and machine learning (ML) are becoming integral to robotics in the automotive industry. These technologies enable robots to learn from data, improve their performance over time, and adapt to complex tasks without human intervention. AI-powered robots can analyze vast amounts of data in real-time, making them ideal for predictive maintenance, quality control, and process optimization.
AI Applications in Automotive Robotics:
- Quality Inspection: AI-driven robots can detect defects in automotive components with greater accuracy than human inspectors. Using computer vision and deep learning algorithms, robots can identify minute flaws that would otherwise go unnoticed.
- Predictive Maintenance: AI systems can monitor the health of robotic equipment, predicting when maintenance is needed before a breakdown occurs. This reduces downtime and increases the overall efficiency of the production line.
- Process Optimization: AI can analyze production data to optimize workflows, reducing bottlenecks and improving the speed and efficiency of manufacturing processes.
In 2024, AI and ML are enabling automotive manufacturers to enhance their quality control processes, minimize waste, and increase production efficiency, all while reducing the need for human intervention.
3. Autonomous Mobile Robots (AMRs)
Autonomous Mobile Robots (AMRs) are another key trend in the automotive industry. These robots are designed to navigate complex environments without human guidance, using advanced sensors, cameras, and AI algorithms. Unlike traditional Automated Guided Vehicles (AGVs), which follow predetermined paths, AMRs are capable of adjusting their routes based on real-time data, making them more flexible and efficient.
AMR Use Cases in the Automotive Industry:
- Material Handling: AMRs are being used to transport materials and components within factories, reducing the need for manual labor and improving efficiency. They can navigate busy factory floors, avoiding obstacles and adapting to changes in their environment.
- Inventory Management: AMRs can also be used for inventory management, automating the process of moving parts from storage to production areas. This reduces errors and ensures that production lines are always stocked with the necessary components.
- Logistics: In addition to material handling, AMRs are being deployed in logistics operations, where they can autonomously load and unload trucks, optimize warehouse operations, and improve supply chain efficiency.
As automotive manufacturing becomes more complex, the demand for AMRs is growing. Companies like Tesla, Toyota, and General Motors are increasingly using AMRs to automate material handling, improve factory logistics, and reduce production costs.
4. Robotic Welding and Painting
Welding and painting are critical processes in automotive manufacturing, and robotics has long been used to automate these tasks. However, in 2024, advancements in robotics technology are taking welding and painting to new levels of precision and efficiency.
Robotic Welding:
Robotic welding systems are widely used in the automotive industry to join metal parts together, creating the frames and bodies of vehicles. These robots are capable of performing high-precision welds at speeds far greater than human workers. In 2024, the integration of AI and machine learning is enhancing the capabilities of robotic welders, enabling them to make real-time adjustments based on the quality of the welds.
- Improved Accuracy: AI-powered robotic welders can detect inconsistencies in the welding process and adjust parameters such as heat and speed to ensure a perfect weld every time.
- Reduced Waste: By minimizing errors, robotic welders help reduce material waste and improve the overall efficiency of the manufacturing process.
Robotic Painting:
Painting is another area where robotics is making a significant impact. Robots are used to apply paint to vehicles with a level of precision and consistency that is difficult to achieve manually. In 2024, robotic painting systems are becoming even more advanced, thanks to the integration of AI and 3D vision systems.
- Consistent Finish: Robotic painting systems can apply paint evenly and consistently, ensuring a high-quality finish on every vehicle.
- Reduced Environmental Impact: Many modern robotic painting systems are designed to minimize paint waste and reduce emissions, making the process more environmentally friendly.
5. 3D Printing and Robotics Integration
The integration of 3D printing and robotics is another exciting trend in the automotive industry. In recent years, 3D printing has become a valuable tool for creating prototypes, custom parts, and even entire vehicle components. In 2024, the combination of 3D printing and robotics is streamlining the production process, reducing costs, and enabling greater customization.
3D Printing Applications in Automotive Robotics:
- Prototyping: 3D printing allows automotive manufacturers to quickly produce prototypes of new components, reducing the time and cost associated with traditional prototyping methods. Robotic arms equipped with 3D printing capabilities can work alongside other robots on the assembly line, creating custom parts on demand.
- Tooling: Robots can use 3D printers to create custom tools and jigs, improving the efficiency of the manufacturing process. These tools can be produced quickly and at a lower cost than traditional methods.
- End-Use Parts: As 3D printing technology continues to improve, it is becoming increasingly feasible to produce end-use parts for vehicles using 3D printers. Robotic systems can automate the production of these parts, reducing labor costs and increasing production speed.
The integration of 3D printing and robotics is enabling automotive manufacturers to create more complex and customized vehicle designs, while also reducing production time and costs.
6. Smart Factories and Industry 4.0
The concept of the smart factory is central to the automotive industry’s future. In 2024, smart factories, powered by Industry 4.0 technologies, are becoming more prevalent. These factories use a combination of robotics, AI, the Internet of Things (IoT), and data analytics to create highly efficient and automated production environments.
Key Features of Smart Factories:
- Real-Time Data: Sensors and IoT devices are embedded throughout the factory, providing real-time data on equipment performance, production metrics, and inventory levels.
- Autonomous Decision-Making: AI-driven systems can make autonomous decisions to optimize production processes, such as adjusting the speed of robots or rerouting materials to avoid bottlenecks.
- Predictive Maintenance: Smart factories use AI to predict when machines or robots are likely to fail, allowing for maintenance to be scheduled before a breakdown occurs. This reduces downtime and ensures that production lines run smoothly.
In the automotive industry, smart factories are enabling manufacturers to produce vehicles more efficiently, reduce waste, and improve product quality. Companies like Audi and Mercedes-Benz are at the forefront of adopting smart factory technologies, using robotics and AI to create highly automated, data-driven production environments.
7. Robotic Exoskeletons for Workers
While much of the focus in the automotive industry is on fully automated robots, another trend gaining traction is the use of robotic exoskeletons. These wearable devices are designed to augment human workers, helping them perform physically demanding tasks with less strain and fatigue.
Benefits of Robotic Exoskeletons:
- Increased Productivity: Exoskeletons enable workers to lift heavier objects and work for longer periods without experiencing fatigue, increasing overall productivity on the factory floor.
- Improved Ergonomics: By providing support to the worker’s body, exoskeletons reduce the risk of injury and improve ergonomics, making the workplace safer and more comfortable.
- Enhanced Collaboration: In situations where fully automated robots are not feasible, exoskeletons allow workers to collaborate more effectively with robots, improving overall efficiency.
In 2024, automotive manufacturers are increasingly adopting robotic exoskeletons to support their workforce, particularly in tasks that require repetitive lifting or awkward body positions.
ALSO READ: Car Sales in the European Union